Hemp and Construction
Construction Elements
Using hemp hurds, we are able to make fiberboards and plywood. Cellulose from the same basic material may be used as an adhesive making the finished product 100% organic, biodegradable, insect resistant and waterproof. Unlike regular wood in the case of a fire hemp does not burn in flames but merely kindles, so in a fact it prevents the fire from spreading.
Fiberboards
These boards are noted to have a finer and more compact outer layer as well as a more homogenous surface making it especially suitable for use in the furniture industry since they are easily coloured, varnished and veneered with noble veneers as well as being able to be glued together along with laminate-ultrapas boards and tepistried. In construction they are mostly used as barriers, protective agents, suspension systems, floor and wall padding,...
Isolation elements
...is made from hemp fiber and is thought to be an ecological equivalent of stone and glass wool which are usually used as insulation for roofs and fasades. Heat insulation of the material is achieved by small air pockets that are naturally formed between particular fibers. Considering heat and sound insulation hemp's features are comparable to stone wool (heat conductivity 0,040 W/mK) but is significantly lighter (lesser density) in considerably more moist resistant which even increases the material's heat conductivity. Its primary advantage being of an ecological standpoint – the entire process of hemp insulation production has a negative carbon footprint, including the energy needed to grow and process the plant itself (unlike stone wool which is made from melting basalt and diabse at 1600°C(!). It is also considered to be more human friendly since it does not contain any artificial substances of additives that would be harmful (i.e. skin and respiratory irritation). By using hemp insulation we also avoid the undesired effect of subsidence and structure deformation due to weight.
Hemp concrete before installation (left), dried and chopped hurds (right)
Hempcrete is an eco-material composed of:
Hemp carrying bricks (with added cement and magnesium) – left: carrier prefabricated panels (adding clay) (Picture 3&4)
Cutting of prefabricated hemp bricks before installment (left), usage of bricks as floor insulationin screed (right); Source: ISOHEMP, Belgium (Picture 5 & 6)
Hempcrete is mostly used as a filler for wooden sceletal constructions which are the same as when building a prefab. In this case hempcrete acts as a filler for walls, roofs and floor that do not bare the pressure of vertical loads due to insufficient tensile strength. On the other hand it is strong enough to take the pressure of horizontal forces (i.e. in case of an earthquake). Further wind protection is therefore not recquired (i.e. with diagonales).
Cross-section of a wall made from hempcrete – wooden pillars are protected from insects and moisture (left), Pounding the material intothe panelling with hammers (right) (Picture 7,8)
Hempcrete may be built in by hand – panelling is set around small pillars and into it a still moist material is applied layer by layer. Using this approach no special tools are needed, nor a substantial ammount of prior knowlede is required the only set back being that this method is somewhat time-consuming.
Recently a more wide-spread method has been in use. With it hempcrete is built in by mechanical injection where a smaller ammount of adhesive is needed, consequentially the wall is more insulated. By injecting hemprete the ingreditents are mixed together during the process itself (although many variations to the theme exist) where adhesive usually exits through one nozzle (lime mixture + water) while small pieces of hemp stem center come from another nozzle. Panelling is set all throughout the wall height behind the pillars and is then onesidedly injected on. After the panelling had been removed the procedure is then repeated from the other side so that the pillars remain firmly set within the construction.
Depending on where hempcrete is being used or the function it is to have, different mixtures of hempcrete may be prepared:
Advantages of building with non load bearing concrete
- A high degree of heat insulation ( λ=0.06W/m.K) : 30 cm thick wall made from hempcrete equals a 30 cm thick wall made from Porotherm which contains 14 cm of styropor (U=0.20 W/m2K). What makes hempcrete special is that it is homogenous and insulative all along the cross section of the construction avoiding the issue of two coexisting materials (of which one is load bearing and the other insulative as with classical building techniques) where the accurance of vapor may be observed.
- A good ability to store heat (1500-1700 J/kg). Once an object made from hempcrete is heated the walls contain the heat and disperse it slowly back into the room.
- Airtightness (2m3/h.m – 2 at 50 Pa)
- High degree of sound insulation (0,69 NRC). Due to its porosity hempcrete is an excellent sound insulator
- Tensile strenght up to 1 Mpa (considering its low density at 330 kg / m3). Although the material is not firm enough to withstand vertical burdens it is strong enough to withtake possible horizontal pressures on the object, i.e. an earthquake.
- Fireproof (73 min with a 30 cm thick wall). Hemp combined with lime simply kindles and in the event of a fire does not bring large flames to life.
- Vapor permeability (the outer wall controls moisture within the room; μ = 4.84). In case of elevated moisture content in the room the wall absorbs it and returns it into the room when moisture levels are low. By doing this it prevents molds from forming.
- Insect resistant (the wooden construction does not recquire any additional protection). Hemp by itself does not have any known natural enemies when growing on the fields – because of this trait the construction wood within the wall is better protected and does not need to be further protected with coating.
- Zero carbon footprint (1m3 of hempcrte stores 130 kg CO2). In fact hempcrete is a carbo-negative material meaning the plant itself binds more CO2 from the atmosphere than is produced by processing. Several years after being built it lime binds some of the CO2 as well due to the process of carbonization – changing its chemical structure back to CaCO3.
- Appropriate for people suffering from allergies. Hempcrete acts as an antibacterial material.
- Thin outer wall – single layer. The outer wall made from hempcrete is made final by using only inner panelling (also made from hemp) and an outer lime panelling. To compare: modern prefabricated houses low-energy houses have an outer wall made from 10 layers.
- Most of the built in material can be locally grown (hemp + wood)
- Fast and easy building process
- Longevity of buildings (there is a building in Japan made from hempcrete which is 300 years old)
- Low construction costs (especially when using your own / local material)
- Could be recycled – material is completely natural and biodegradable
- Positive side effect of rotation with hemp on surfaces darined of organic layer or poisoned from intensive use of pesticides and artificial fertilizers.
- Versatile use of the entire plant (i.e. seeds for food, fiber for textile and flowers for tea) therefore no waste is produced
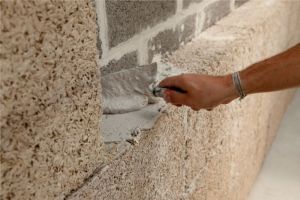
Konopljin beton (hempcrete)
Konopljin beton je ekološki material, ki ga sestavljajo: konopljin pezdir (sredica konopljinih stebel, ki jo sestavlja pretežno celuloza), apnena mešanica (sestavljena iz gašenega apna, naravnega hidravličnega apna NHL5 in cementa) ter vode. Konopljin beton se večinoma uporablja kot polnilo lesene skeletne konstrukcije, ki je enaka kot pri gradnji montažne hiše.